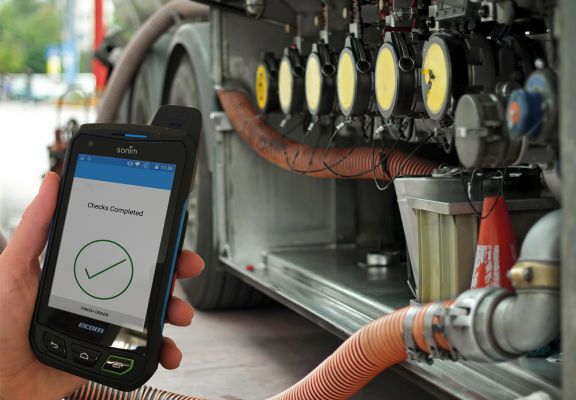
CheckScheme was created when Inter Terminals, a client of MHT Technology,
collaborated with them to find a solution with their current operations.
The dangers of manual paper-based checks became evident to their
client when they assessed their operations for risks. Despite years of
experience, they recognised there is always the possibility of shipping
the wrong product to a customer. A simple mistake can result in
the forced shut down of the customer’s site and the destruction of
contaminated stock. Operators using paper-based systems often become
unintentionally complacent using the same procedures day after day
resulting in shortcuts being taken.
Inter Terminals CASE STUDY
…PEOPLE ARE NOT ROBOTS
Damian Wroblewski, Operations Manager from the largest independent bulk liquid storage provider in the UK, Inter Terminals, gave a presentation on how CheckScheme was created in collaboration with MHT. A long-time client of MHT, Inter Terminals suggested the idea of CheckScheme originally to provide a robust checking system which reduces the level of human error during product loading or discharge processes.
Damian Wroblewski commented; “When working for many years people turn onto autopilot. People are not robots: they might be tired, they might be bored, and find the job mundane. We must take the human factors into consideration, we are not perfect, however in this business one mistake might lead to a serious disaster. You can’t be distracted, even for a second.”
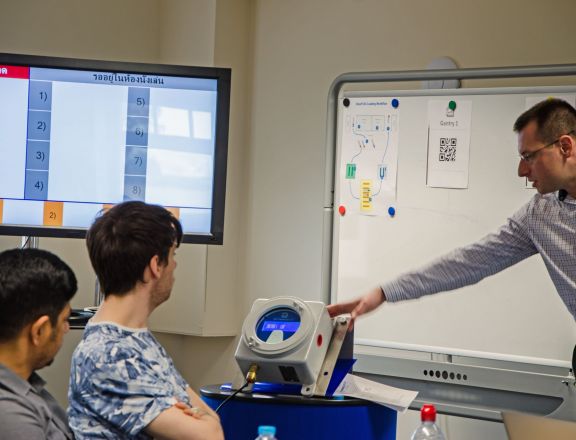
Damian Wroblewski – Inter Terminals
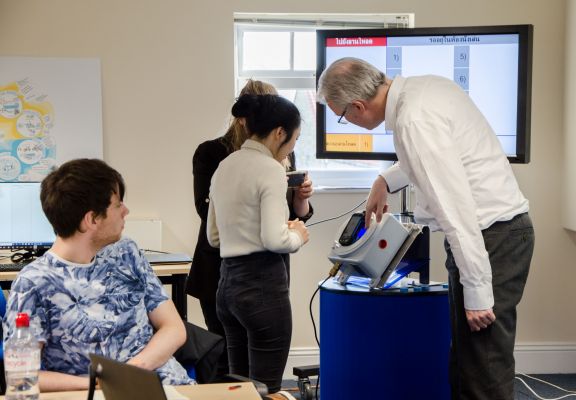
Paper-based operations also have a disadvantage when capturing data.
Although paper checklists are usually filed away after completion they
can be misplaced, and the data is not open for analysis to enhance the
operations further. HSE favours clear and precise documents to evidence
that correct procedures have been followed. Having that evidence in a
digital format makes it much easier to track and locate specific data.
CheckScheme accommodates existing operations allowing cost-effective
migration to a digital platform, with human factor at the forefront of its
design.
DEVELOPING CheckScheme
“‘The system concept was developed with our customer, at first we approached the problem by trying to develop a heavily engineered solution. ATEX Zone 1 electronic devices that linked back to servers at the site that would be interrogated when an operator wanted to load a truck. It soon became evident that this required lots of effort, the cabling alone represented weeks of work.”– Marcus Webster
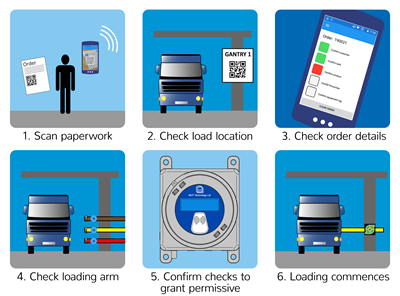
We then realised that the problem wasn’t that the equipment at the site needed to be controlled, it was that the operators needed a way of establishing that they are doing the right thing. No one turns up to work expecting to make mistakes or work unsafely.
MHT engineers then devised a system that used a smartphone to guide the operators through a checklist, before confirming visually to the operator that the checks had been passed. It was realised that a checklist on a smartphone could do more than just ticking a box; operators could scan QR codes, RFID tags as well as answer questions about the job they are undertaking. Webster adds: ‘Being much more than checklists, we named them ‘Check Schemes,’ this realisation that check schemes could be applied to many procedures on-site, not just loading trucks and it inspired us to get behind the product and develop it further.’
Checkscheme in action
The CheckScheme system consists primarily of a server, which can either be deployed in the cloud or on the customer’s own premises. Operations managers access the server using a web browser, and from there can configure and manage the site’s check schemes.
The CheckScheme app is installed on Android mobile devices, which are registered with the server over a Wi-Fi network. The Wi-Fi network does not need to cover the whole site, as the system is designed so that operations can be carried out without any immediate contact with the server. When the phone is within range of the Wi-Fi network, it synchronises with the server, allowing the latest versions of the check schemes to be downloaded to the phone, and the activities the phone has performed to be uploaded to the server. Webster explains: ‘For example, by installing the Wi-Fi access point in the staff canteen, the operators can hand in their checklists and receive changes to procedures while enjoying their morning cup of coffee.’
The operator begins by scanning a QR code printed on the works order. The QR code is generated by either filling in a form on the server or by integrating CheckScheme with company ERP systems via an API on the server. The QR code identifies the check scheme to use, a reference number for the activity and the expected values the operator will give. The operator steps through the checks one-by-one, an incorrect response prompts the operator to try again, while correct responses confirm that the operator is at the right loading bay or using the right loading arm.
When the final check is completed successfully, the operator is given a clear confirmatory message. If a physical control is used, the smartphone is presented to the controller and a permissive relay is closed allowing the machinery to be activated.
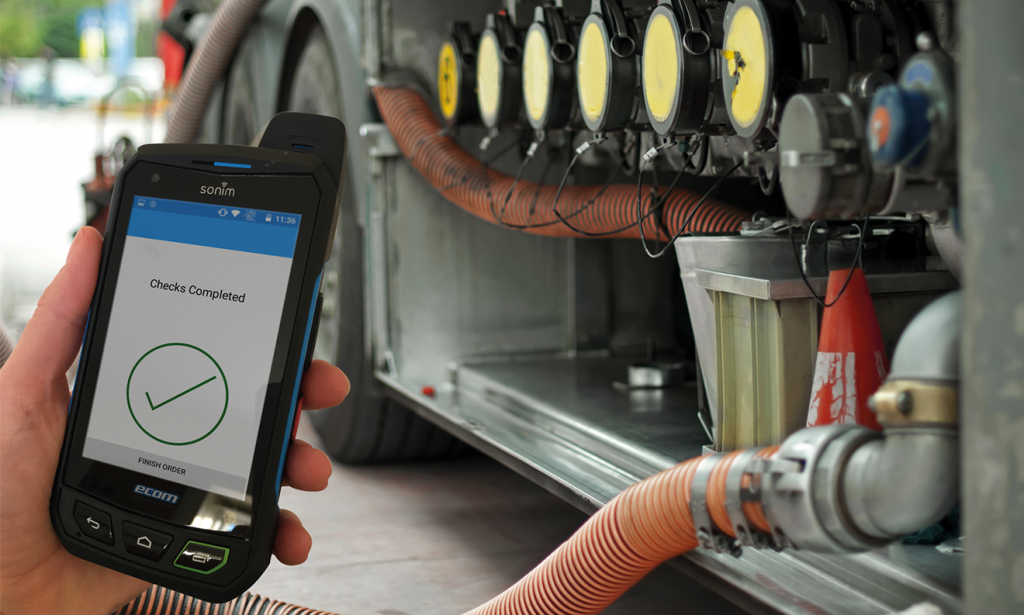
MANAGING PROCESSES WITH CHECKSCHEME
The data uploaded to the server includes a timestamped log of events that have occurred while using the app, including any incorrect responses the operator has given. Supervisors can examine the handling of a specific order to confirm issues regarding delays completing the procedure. They can also report statistics for the performance of processes. Check schemes are subject to workflow within the system. This gives the operations manager the ability to create a new check scheme, test it, then get it approved for use and retire old schemes at the end of their life.
Paper-based systems while being cheap to implement, are difficult to change and maintain. This leads to a reluctance to improve procedures, resulting in missed opportunities for safer and more efficient working.
The latest features in CheckScheme allow for the recording of richer data and scheduling repetitive tasks. The system can still make use of RFID tags and QR Codes to identify locations and equipment, but now textual and photographic information can be recorded. For example, CheckScheme users can record photographs of the laden vehicles before they leave the site, to be able to show that they have discharged their duties in line with ADR and ensure every vehicle with a hazardous load leaves your site carrying the correct placards and markers.
The built-in calendar allows processes to be scheduled. Tasks such as manual tank dips can be scheduled to occur at regular intervals, capturing the levels recorded easily with the mobile device. An RFID tag placed on the roof of the tank which the device reads ensure operators can’t falsify readings. The server shows the results, permitting gauge drift to be assessed.
CheckScheme is an outstanding digital solution. Not only because of how the algorithm and potential technology behind it has been maximised but also because of how the human factor sits at the core of the solution right from the beginning. When it comes to digitalisation, there is a great tendency to see only data and technology at the core, but MHT strongly believes the human element is equally important and key. With the aid of CheckScheme, operators can make the handling of hazardous materials such as petrochemicals, fuels, and chemicals, controlled, measured and safer, reducing the human element of risk associated with product loading and discharging processes. All without sites investing in expensive automation projects that disrupt operations and increase maintenance costs.