Overview
LMS keeps your LNG as safe and profitable as possible. LNG is a rapidly growing source of power across the world but brings with it many unique challenges. When differing compositions are stored in the same tank stratification can occur. If left unmanaged stratification can result in a rollover with catastrophic consequences, such as loss of containment, loss of reputation and loss of life. LMS manages your site, giving a clear analysis of tank profile data, giving real-time notification of stratification.
Our rollover prediction software further analyses the data to generate forecasts of the tank state. This enables LNG to be sourced from different sources and stored safely; giving terminals significant cost savings.
The LMS system has been designed to interface to all instruments commonly found on LNG storage tanks, and to collect and present the instrument data through a range of intuitive graphical user interfaces. A typical LNG Tank will have a wide range of measurement instruments to measure Liquid Level, Liquid Density, Liquid and Vapour Temperature, Liquid and Vapour Pressure, Skin Temperature and much more.
Typically, each tank would be fitted with an LTD gauge, two further level gauges configured as a Primary and Secondary and an Alarm Gauge. The LTD gauge is a servo-operated unit mounted on the tank roof. The purpose of the LTD gauge is to take accurate profiles of temperature and density throughout the liquid, and whilst not profiling provides a continuous liquid level, temperature and density measurement.
The Primary and Secondary gauges can be either servo and/or radar operated units also mounted on the tank roof. The purpose of these gauges is to provide continuous liquid level measurement and average liquid temperature measurement. They provide redundancy on the measurement of level and temperature. The average liquid temperature is derived from a multi-point temperature sensor device.
The alarm gauge is often a servo or radar-based gauge configured to provide volt free contact alarm status to an independent system. The alarm gauge is often connected to the LNG tank management system so that its operational status can be monitored. An LMS system can operate in a simple standalone configuration or as a fully redundant system where security and integrity are of paramount importance.
The hardware part of the LMS system, the Mini Receiver, a serial data concentrator and protocol converter. This device can interface to a wide variety of different instruments. The LMS system has a flexible and scalable architecture allowing it to be tailored to different applications easily.
LNG benefits
Cleaner
cost savings
safe
easy to transport
software features
LMS has undergone a process of continual innovation over 11 years, often incorporating feedback and requests from the customers that use it. All our software is designed, developed, and tested in-house by a team of bulk liquid storage and handling experts.
All measured and calculated tank parameters are accessible to your tank farm and terminal operators as well as to connected host systems. Multi-user operation is provided by the inbuilt Web Server offering the opportunity to access data at any connected location (local/remote) e.g. for administrative and accounting purposes.
The latest features of LMS includes
- Live data.
- Calculated data.
- Real-time and historical trending.
- Alarm management and annunciation.
- Instrument support, Host Interfacing.
- LNG Rollover Prediction model.
Automatic LNG Composition Selection.
LMS benefits
Data mining
Integration
Reliability
EFFICIENT
Redundancy
remote working
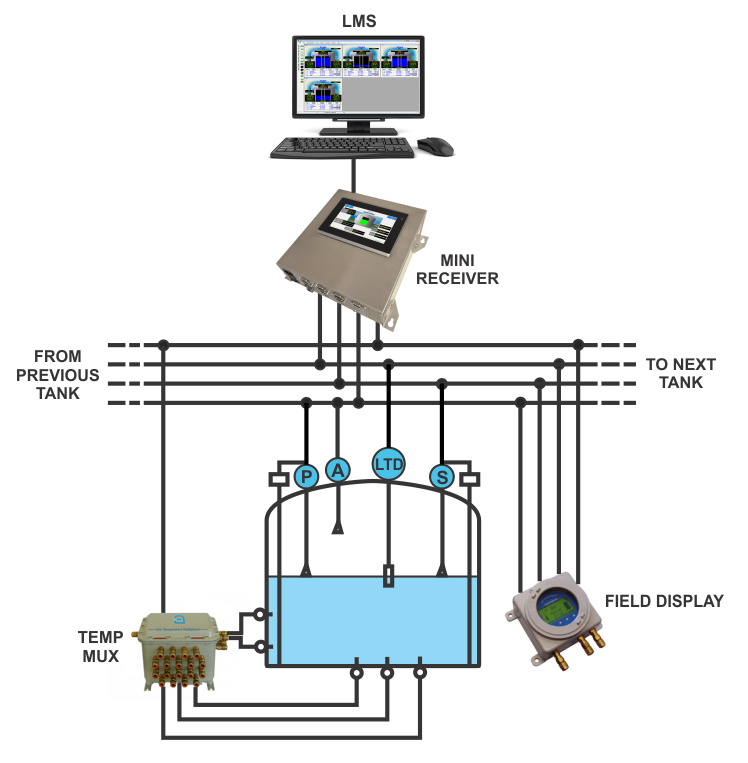
Standalone configuraton
A PC running LMS is connected to a Mini Receiver via either a Serial Data or Ethernet connection. The Mini Receiver is then further connected to the field instruments via field bus interfaces. The Mini Receiver can be configured to provide a wide range of different electrical interfaces allowing it to be connected to many different vendor instruments.
Redundant configuration
The illustration shows a typical redundant configuration with two PCs and two Mini Receivers. In the event of a failure, the redundant machines are used to maintain system functionality.
The degree of redundancy and architecture of the system is dependant to some extent on the redundant features of the instruments. Some instruments provide dual outputs so that they can be connected to two independent hosts. In the illustrated configuration on only one Mini Receiver can be active, the other must remain passive. If all instruments had two outputs both Mini Receivers could be active simultaneously. Normally both PCs will be collecting data from the active Mini Receiver and it will be polling all field instruments, the passive Mini Receiver will read data from the active one to make a “hot” switchover possible. Should the live Mini Receiver fail, the other Mini Receiver will take over the polling of the instruments and the PCs will look to the other Mini Receiver for data, hence maintaining the operation of the system.
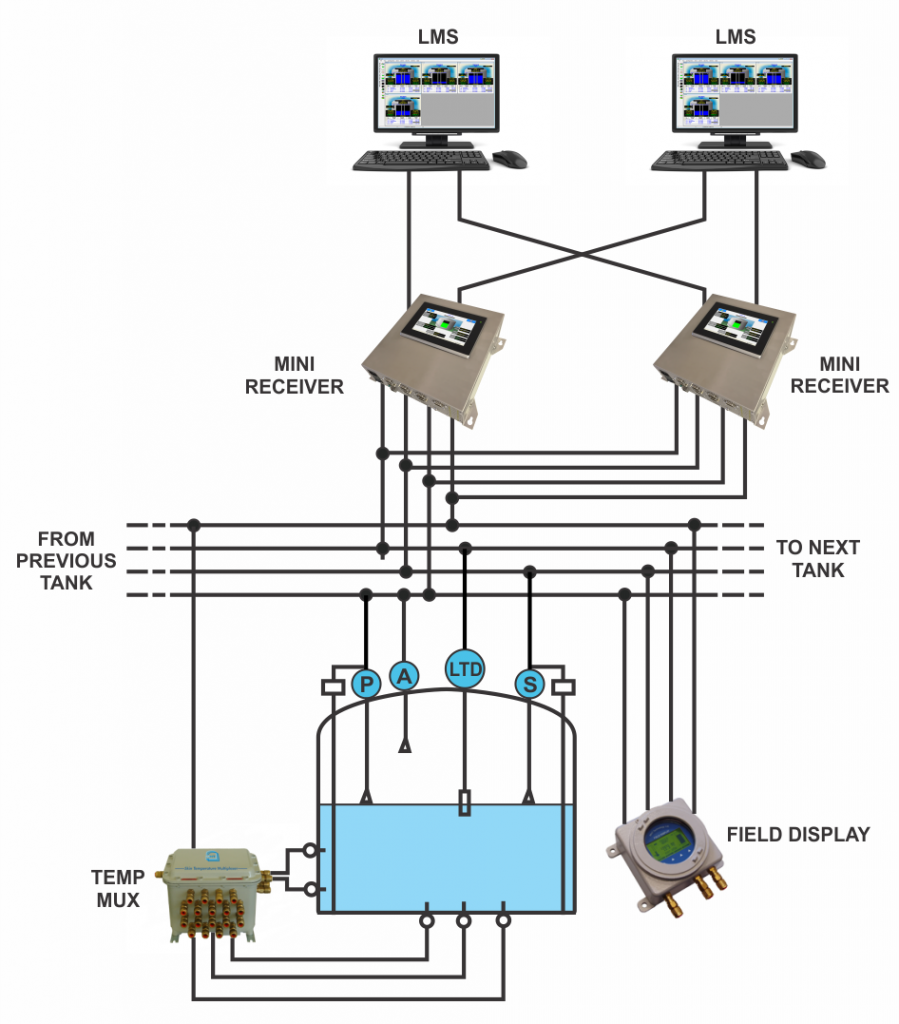
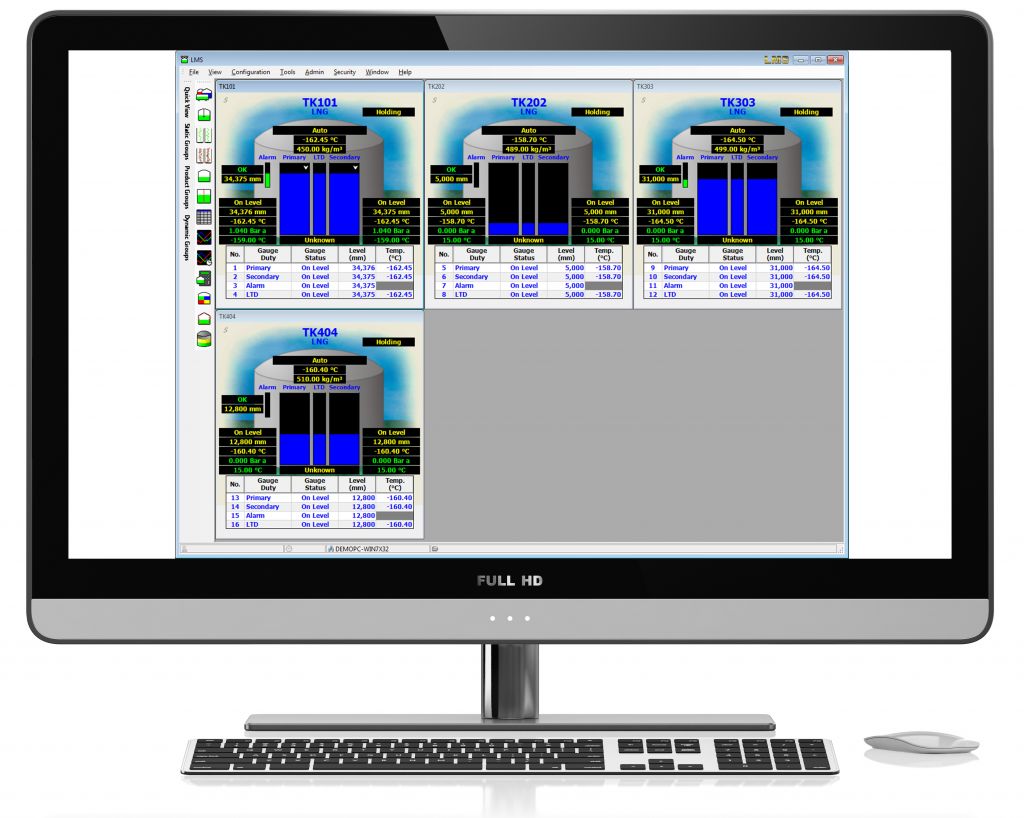
Live data
LMS can be configured to poll the tank instruments for a wide range of data values. The actual data available in any application depends on the instruments and their capability.
In general, the following live data is collected:
• Liquid Level
• Average Vapour Temperature
• Average Liquid Temperature
• Current Liquid Density
• Vapour Pressure
• Skin Temperature (Optional)
On a scheduled basis the following additional live data
can be collected:
• Level, Temperature and Density Profile
Calculated data
LMS can be configured to calculate certain inventory parameters for each LNG tank. To calculate inventory each tank must be
provided with a tank calibration table.
In general, the following inventory parameters are calculated:
• Total observed Volume
• Gross observed Volume
• Ullage Volume
• Gross Mass
• Ullage Mass
• Liquid Mass
• Vapour Mass
• Calorific Value (Optional)
• Wobbe Index (Optional)
• Energy (Optional)
• Multiple trends
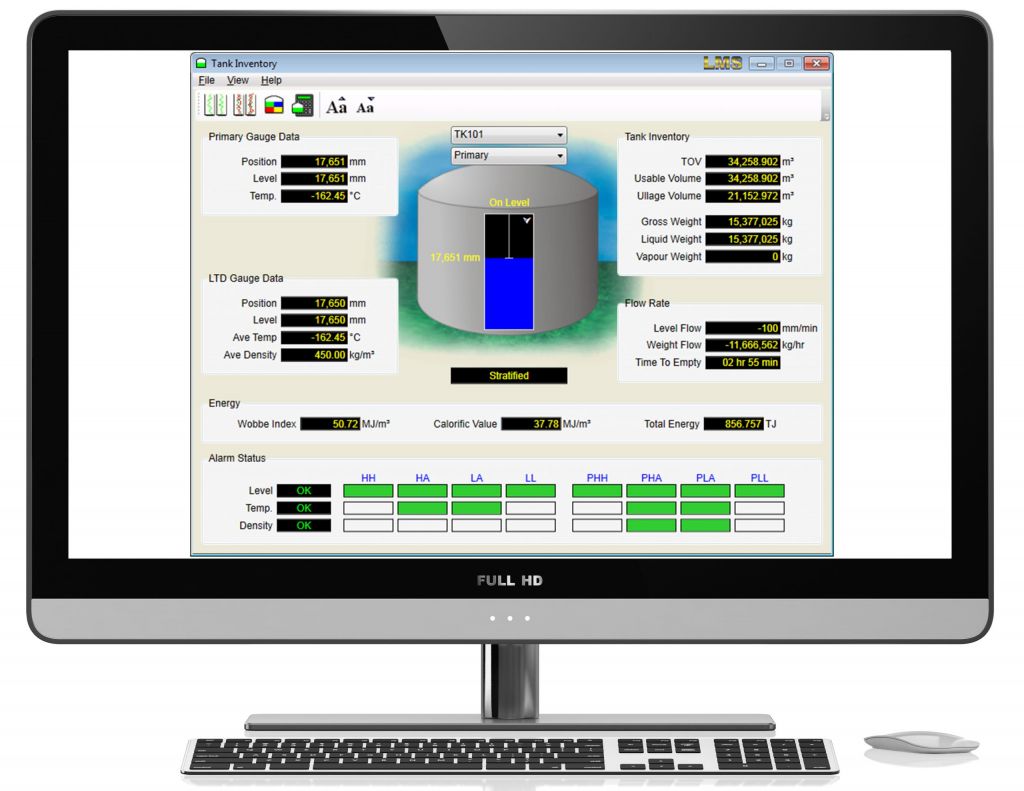
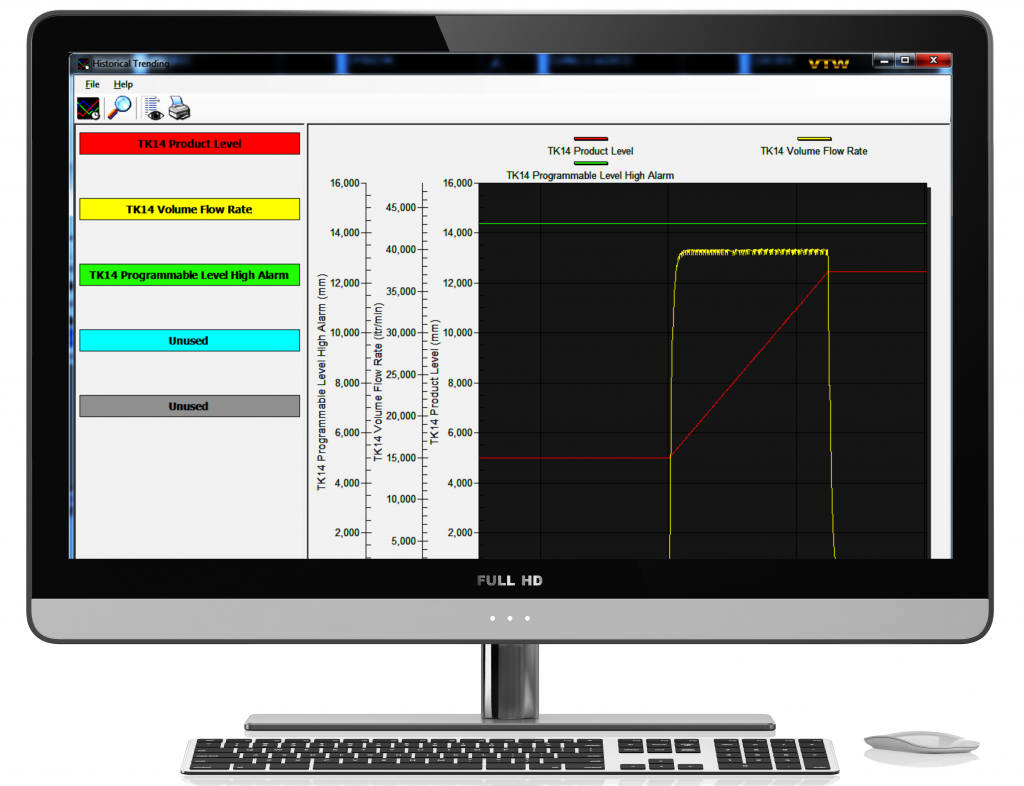
Real-time and historical trending
LMS has an integrated trending module that logs live and calculated data for all instruments to the computer’s hard drive. Through the intuitive graphical user interface the user can view trend data in real-time or as a historical trend view. Multiple trends can be placed on the same graph showing different data values for the same, or different tanks. A data cursor can be placed on a trend to view the numerical value at a particular date and time. The trend features are excellent tools for analysing the performance of instruments and tracking product movement in tanks.
Alarm management and annunciation
LMS has integrated alarm management and annunciation on a system that can be customised to meet the requirements of most sites.
All alarms are time and date stamped and logged to a database. Each alarm can be configured to optionally, play a sound or voice message, require acknowledgement, send an SMS or e-mail, plus much more. Alarms can be prioritized by severity so that the highest severity alarms cannot be masked by lower severity alarms.
Alarms are typically available for the following conditions:
• High-High, High, Low, Low-Low, Level Alarms
• High/Low Flow Alarms
• High/Low Temperatures and Density Alarms
• Stratification Detection on Alarm
• Temperature/Density profile, Deviation Alarm
• Unauthorised Movement Alarm
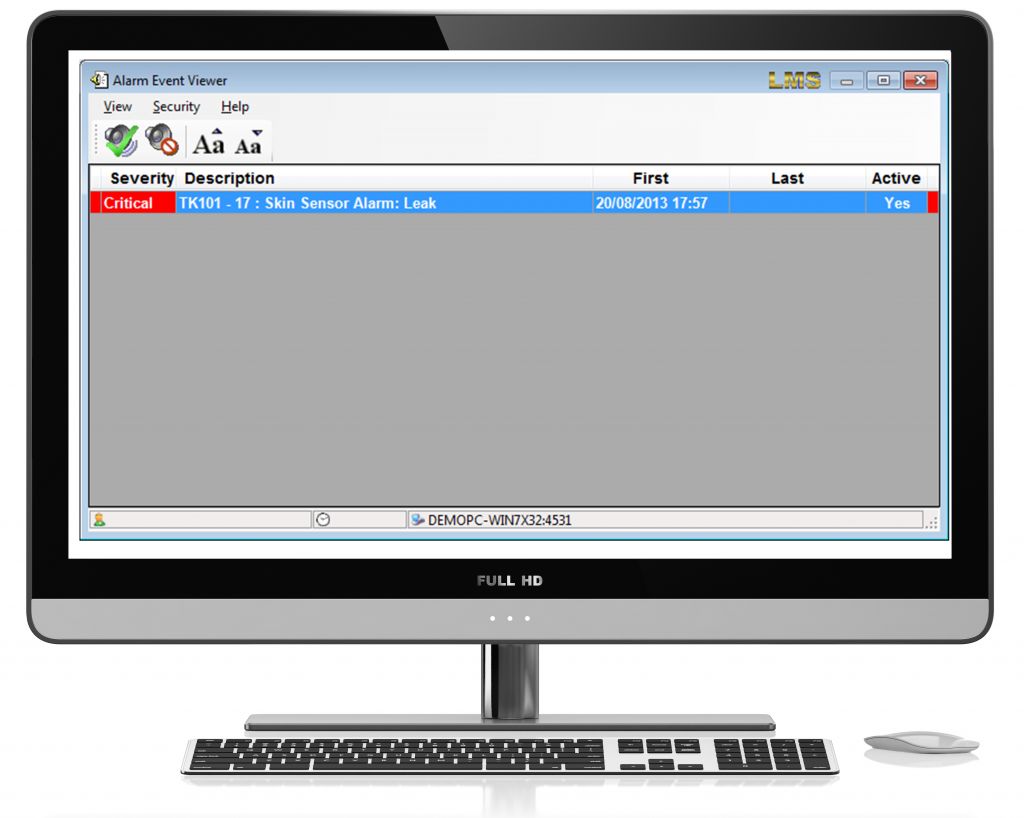
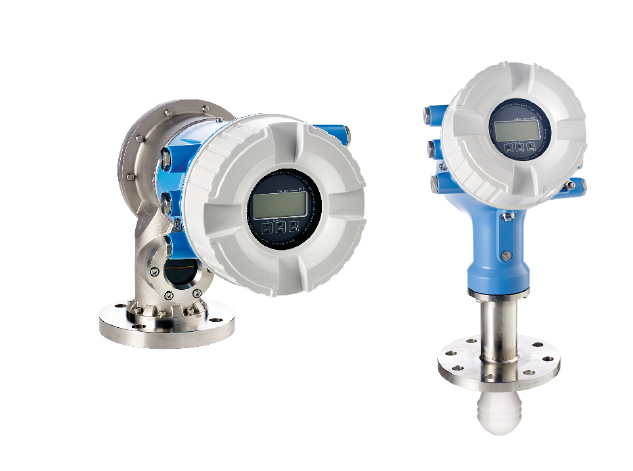
Instrument support
LMS has the ability to support a wide range of different instruments.
The following gauge types are supported:
• Scientific Instruments 6280, 6290, 7000 ®
• Honeywell Enraf Servo / Radar ®
• ‘Saab’ Emerson Radar ®
• Endress+Hauser Proservo / Radar
• Whessoe 146 LTD
Host interfacing
In many applications, LMS forms an essential part of a bigger system. Consequently, it is necessary to provide data to a number of host systems. LMS can be configured to provide data to a host in the following formats:
• Modbus RTU
• Modbus TCP
• OPC
• ODBC
LMS can support multiple host connections. The Modbus and OPC connectivity are read and write allowing the host to download data and send gauge commands.
LMS has been interfaced to many host systems some of which are listed below.
• Honeywell TDC ®
• Foxboro I/A ®
• Yokogawa ®
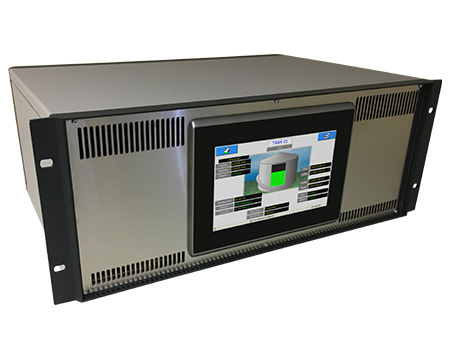
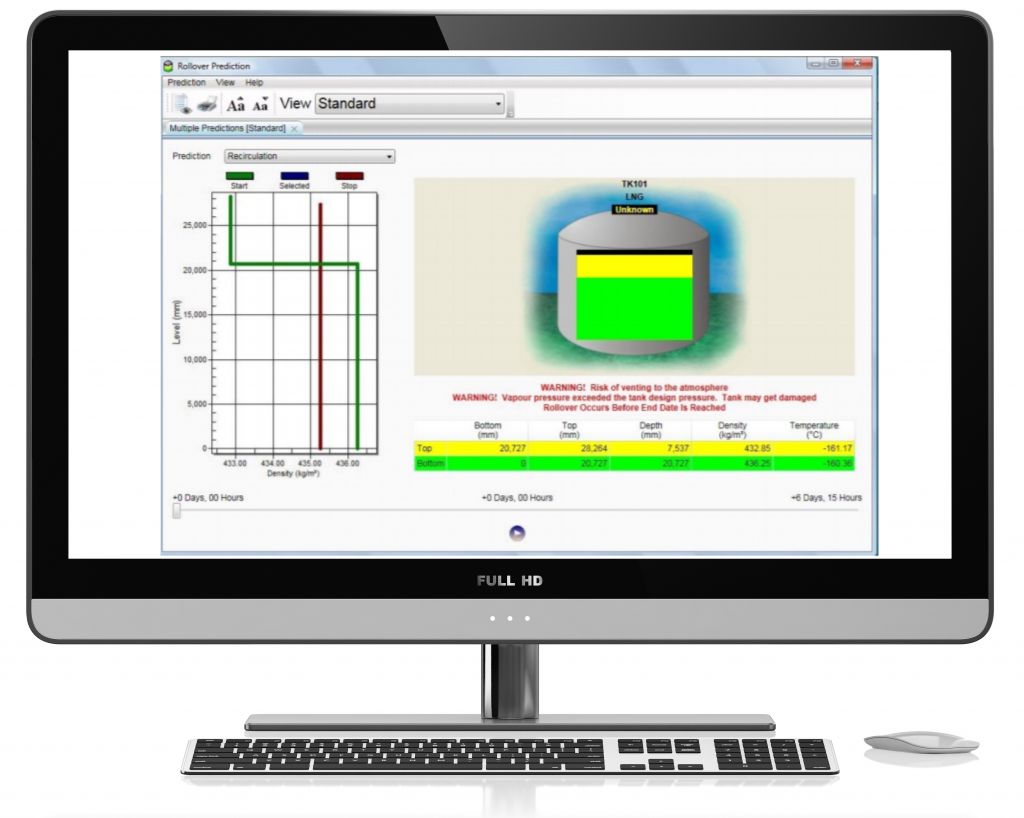
LNG Rollover Prediction model (optional)
This model allows the user to visualise the evolution of temperature, density, boil-off and the layer thickness of the stratified layers within an LNG tank. The model can be run with either manual or live data and is a fully integrated feature of the total LNG Tank Management solution. If the model predicts a potential rollover, the model will display the time to rollover as a rollover alarm. The time to rollover and the stratification status can be transmitted to the site DCS for further annunciation. A feature of the rollover prediction model is its ability to infer heat and mass transfer coefficients from the real-time LTD profiles. The rollover predictions are sensitive to heat and mass transfer coefficients that control mass and energy transfer between the stratified layers. In MHT’s software, the heat transfer coefficient can be entered manually by the user (manual mode) or can be inferred from an inbuilt empirical correlation (empirical mode). The third mode, called inverse mode, estimates heat and mass transfer coefficients from the real-time level/ temperature/density (LTD) profiles. MHT Technology was the first to market with this feature which was developed in association with Sheffield University.
Automatic LNG Composition Selection
New to 2020, our new feature automates the process of forecasting rollover in LNG storage tanks. In previous versions of the software, it was incumbent on the operators to make the best guess as to the composition of the LNG in the storage tank by setting it following a receipt of LNG into the site. With the Automatic LNG Composition feature in Tankvision LMS the density and temperature measured by the LTD gauge is matched against a database of known compositions.
The composition of the LNG in the tank is a critical input to the rollover calculation. The ability of the species in the LNG to migrate between strata and the differences in thermal expansion of those species in the layers affect the time taken for density equalisation to occur. For an accurate forecast, it is therefore essential that the correct composition is fed into the model’s input parameters.
Tankvision LMS provides site managers with the tools to maintain a list of LNG compositions that their site will handle. This database is set up during commissioning and subsequently updated when new sources of LNG are imported into their terminal. Crucially, unlike some vendors who charge for updates to the composition database, sites can easily enter details of new gas fields into Terminalvision LMS. For export terminals and peak shaving sites, this database is unlikely to change within the lifetime of the system; for import terminals only when a new LNG source has been selected.
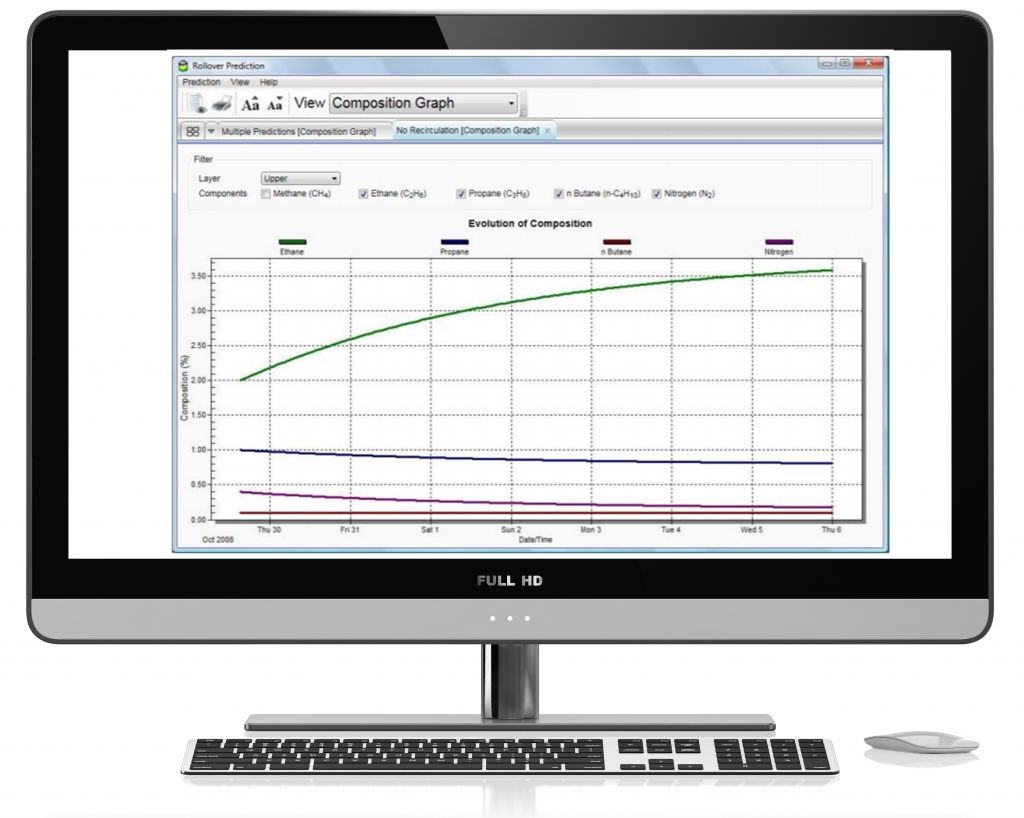
The composition selected by the automatic system is further refined in the model by “tuning” the starting composition to match the actual temperature and density of the layer. It is expected that the composition of the LNG in the storage tank will change over time: there will be some mixing of the layers and preferential boil-off of the lighter species from the upper layer. The model tunes the input composition as part of its process, the automatically selected composition serves only to act as a starting point for the calculation.
find out how LMS can help your site today
DATASHEETS
LMS LNG SOFTWARE
A total LNG Tank Storage and Management solution for Peak Shaving, Receiving and Production LNG Facilities.
What is LNG used for?
LNG is Liquified Natural Gas, or Methane cooled to cryogenic temperatures. When liquified the gas is 600 times denser than it is when a gas, which means that it is more efficient to transport it over water than by pipeline. Generally, the LNG is “regassed” by warming it before use. Most of the world’s LNG production is used in power stations to make electricity or supplied as mains gas to the general population.
What is the difference between LPG and LNG?
LNG is Liquified Natural Gas; LPG is Liquefied Petroleum Gas. Chemically, LNG is predominantly (above 90%) Methane, LPG is a family of products that mostly blend Propane and Butane in various compositions. Physically, the most distinguishing characteristic is the boiling point of the liquids: Methane boils at -161.48 °C, Butane boils at -0.5 °C.
How is LNG Produced?
Most LNG production in the world comes out of the ground from gas fields. The gas is taken from the field by pipeline before being cleaned, compressed and cooled at an LNG export terminal.
Is LNG safe?
LNG creates some risks which must be managed by sites that handle it. The risks which exist at a site are the potential for explosions from the large amounts of methane, and the physical size of the plant at the site. The companies that run these sites are subject to intense scrutiny from local authorities to ensure the safety of the wider community.