Overview
SmartTAS is an intelligent Terminal Automation Solution which gives you total control over product movement and stock reconciliation. Since launching in the UK in 2011, SmartTAS has grown worldwide, allowing our customers to transport bulk liquid with the highest efficacy.
The latest features on the software enhance digital transformation by meeting current demands in the industry. Our mission is to continue making the transportation of bulk liquid as efficient as possible.
Bulk liquid distribution whether by road, rail, air or water requires tight controls to ensure safe, secure and efficient operations. Every site has its own unique set of circumstances that brings with it challenges commercially, environmentally, and logistically. A “one size fits all” approach to terminal automation is impossible however SmartTAS is scalable to the size and requirements of sites. As such, we can offer a simple standalone station for a small depot or scale up to a full client server system for larger sites requiring multiple operator stations.
SmartTAS offers flexibility in its application, supporting many of the leading batch controllers. Access control devices and identification methods are also available to ensure your product is kept safe.
SmartTAS allows full stock management and reconciliation system, with comprehensive reports, BOL to ADR as standard. It enables total site control and overview, allowing operators to access details of all gantries, loading arms, vehicles, drivers, and product in use on-site with ease.
Kiosks and queuing provide load planning and optimisation features with automated notification by SMS and electronic document delivery making operations transparent to stakeholders. API’s allow integration with ERP systems to allow an accurate exchange of transactions and orders, ensuring that the products dispensed are subject to financial controls.
benefits
Real-time and Historical data
automatic reports
Security
KIOSK and queuing
configuration
Integration
technical support
COST SAVING
software features
SmartTAS has undergone a process of continual development, often incorporating feedback and requests from the customers that use it. All our software is designed, developed, and tested in-house by a team of bulk liquid storage and handling experts.
The latest version of SmartTAS includes; support for LPG operations, including improved gas calculations, TGSV as a reconciliation quantity, support for loading from manifolded tanks, returned vapour product and topping up at the loading bay.
SmartTAS can publish live loading bay information, including transaction data such as driver names, order numbers, and vehicle registrations. Integration to 3rd party systems is now possible through the OPC UA interface.
When things go wrong at site, SmartTAS now allows operators to prepare documentation for vehicles that have been manually “topped off” or moved to another loading bay to complete a load.
Core Functionality
- Product Transactions
- Orders
- Products
- Drivers/ Personnel
- Vehicles, Companies
- Gantry, Configuration
- Device/ Instrument Configuration
- Kiosk/ Queuing
orders and transactions
An order represents a right to load for the vehicle and confirms an agreement between parties for the exchange of products. A full stock management and reconciliation system is available with our software. Orders can be simply input through the SmartTAS user interface, or for sites with a higher volume of orders, they could be imported from an ERP system. Sometimes these agreements can be very specific, defining the amount, the product, the compartment, the vehicle and the driver. Sometimes the order can be loose; a customer can take up to a maximum amount of product. SmartTAS can handle those and any cases in between.
On arrival at the site, the driver will select the associated order number and all load details are downloaded to the loading computer to enable the loading process.
Order numbers are created ahead of time in TAS to control the quantity and product for each truck and compartment. This method provides a safe approach for the driver and reduces the risk of loading incorrect quantities or products into the wrong compartments. Alternatively, loads can be created and authorised on demand by the terminal operators upon the arrival of a truck/driver, and all details are recorded immediately within SmartTAS. Addresses are now first-class data items in TAS. A customer can have many addresses associated with it, each being ascribed a role, such as Billing Address, Delivery Address, Safety Contact Address.
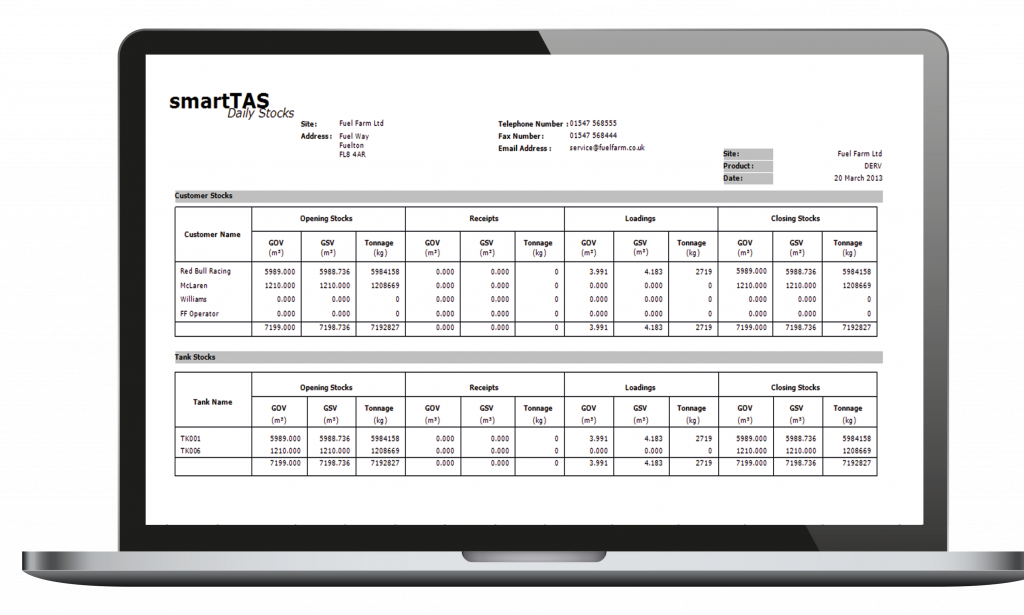
SmartTAS provides a visual representation to the operator of all active data, displaying the loading process with all information associated with the selected order. A full log of all loading transactions is maintained by the automation system, and the Book Stock module gathers all input data for reconciliation of stock. Automatic BOLs are printed at a location on completion of a transaction.
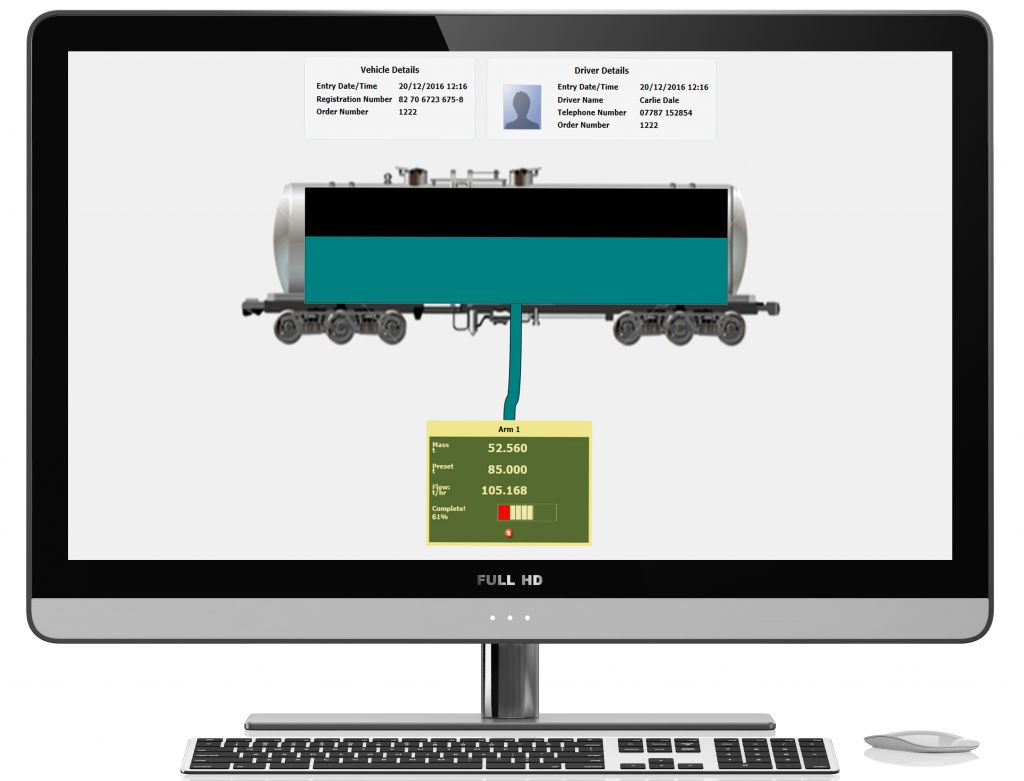
Identity and Access Control
A cornerstone in terminal automation is to know who and what is taking or delivering the product so that responsibilities are established at every step with optimal security. SmartTAS can work with a range of RFID cards and access control units. Biometric checks can be added to further confirm the driver’s identities and prevent “card sharing”. Details of drivers and vehicles can be managed through the SmartTAS application, or through integration using the API.
- The system can interface to most types of Access Control Units controlling both entry and exit of trucks, pedestrians and personnel.
- A full transaction log of all entry and exit requests and activity is maintained in the database.
- Detailed views of all people and vehicles on site are easily accessible in SmartTAS, both real-time and historical.
- Historical records can be queried to analyse personnel, driver and or truck movements.
- Multiple security options: PIN and Swipe card options are fully configurable, or security can be disabled altogether.
- Features can be fully customised to the site’s requirements.
Checkpoints, Loading Bays and Site Locations
At the loading bay the identity of the driver and vehicle can be confirmed ensuring that the right products are dispensed in safe quantities to the vehicle. SmartTAS can check the capacity of the vehicle compartment to prevent overfilling and check the order quantity to prevent oversupply. Inline blending and additive injection are also supported, allowing a diverse range of products to be delivered from a site to order. Further controls and checks can be added using checkpoints to ensure procedures such as bottom drain and seal fitting are carried out. SmartTAS logs the vehicles’ progress through the site locations.
Our continued quest to bring the world’s loading bay equipment into the SmartTAS software sees the addition of seal details being entered at the bay, and support for the Danload DL8000 in a multi-arm deployment. When things go wrong at site, SmartTAS now allows operators to prepare documentation for vehicles that have been manually “topped off” or moved to another loading bay to complete a load.
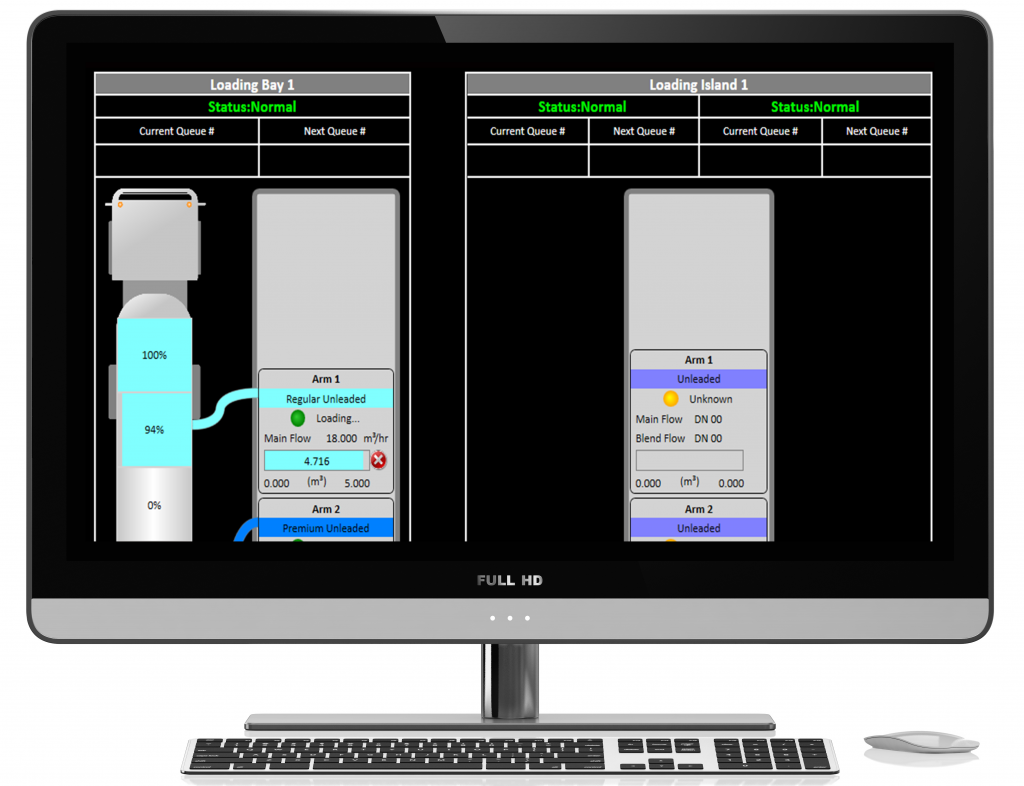
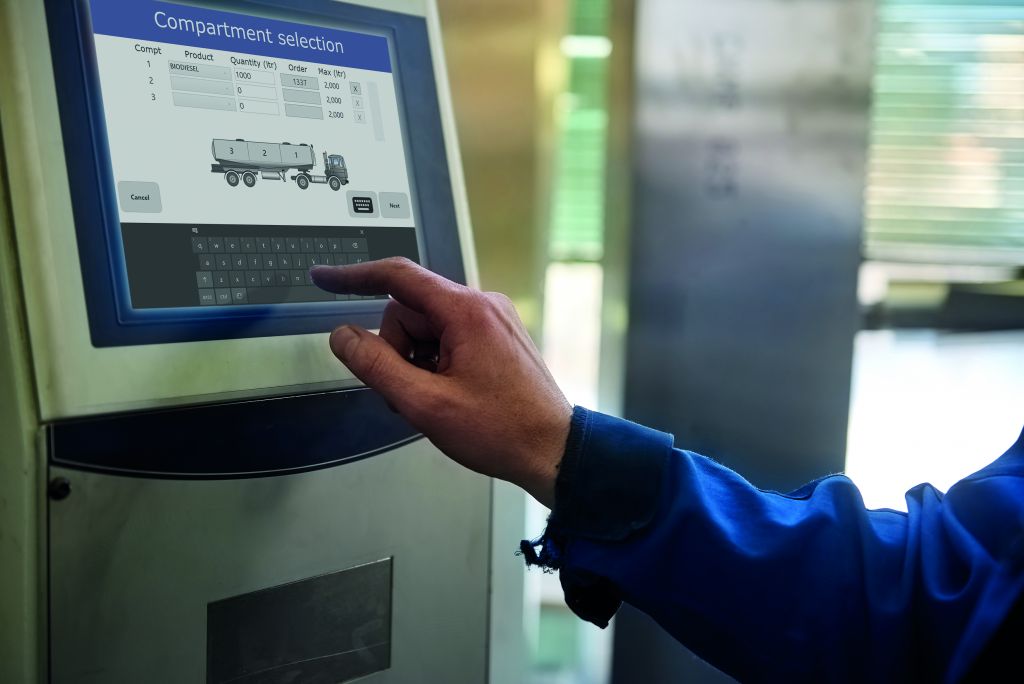
Queuing
To minimize the time the vehicles spend in hazardous locations in the site and prevent unnecessary traffic a queuing system is must. Drivers enter the queue by setting up their load at an automated kiosk, before waiting to be called by the queuing system. A queue status screen in a waiting area ensures that people are kept in a safe location and only venturing on to the site when needed.
System Architecture
• Standalone station
• Client-Server system
• Distributed multi-site systems
• Modbus and OPC interfaces to sitewide
distributed control systems and other
business systems
• Fieldbus and device-independent
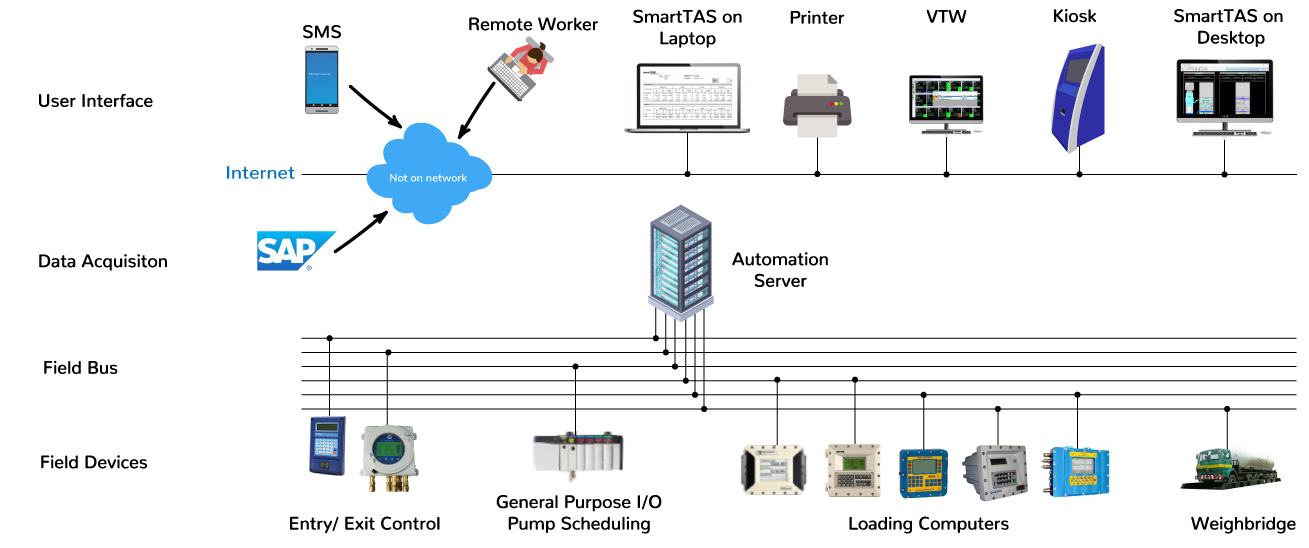
find out how SMARtTAS can help your site today
DATASHEETS
smarttas terminal automation Software 18.3.3
SmartTAS is a flexible Terminal Automation Solution which gives you total control over product movement and stock reconciliation.