Overview
We believe paper-based checks are dangerous and MHT’s mission is to eliminate them. CheckScheme digitises paper-based checklists, enabling operators to carry out their checks quickly and efficiently with an easy to use smartphone app. Drop the lengthy paper-work, out of date procedures and missing documents. Chechscheme replaces vulnerable paper-based systems with a centralised way of managing the important checklists that operators carry out day to day in hazardous environments. Digital transformation is at the centre of Checkscheme, but with the human factor at the core by creating smart and compact data which operators can access and change instantly and update their checks simultaneously to the cloud. With the power of Checkscheme, Operators now have the ability to receive accurate and more reliable evidence that procedures have been followed correctly in the event of an accident. It enables you to involve and motivate your team more to successfully complete their process.
The system supports the needs and requirements of each site by allowing flexible and quick deployment of safety checks. The SOC (Safe Operation Controller) is an optional physical component of the CheckScheme system that ensures the right checks are being followed. CheckScheme was created when we collaborated with one of our customers to find a solution with their current operations. The dangers of manual paper-based checks became evident to their client when they assessed their operations for risks. Despite years of experience, they recognised there is always the possibility of shipping the wrong product to a customer. A simple mistake can result in the forced shut down of the customer’s site and the destruction of contaminated stock. Operators using paper-based systems often become unintentionally complacent using the same procedures day after day resulting in shortcuts being taken.
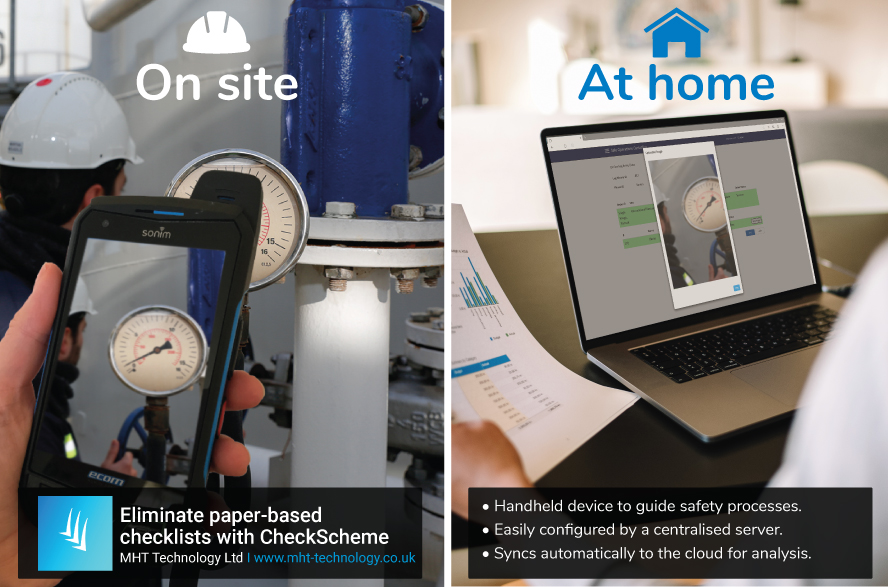
Dangers of paper-based checklists
Inefficiency
No certified record
No data mining
No physical element
No control
Human errors
software features
CheckScheme raises your operational standards in every aspect of its design. MHT’s app for ATEX certified Android smartphones gives clear and instant feedback to the operator, displaying a green icon for successfully completed checks and a red icon to highlight any errors made, providing the ability to instantly correct the mistake before the next stage.
Operators can verify they are at the right site location by scanning a QR code on signage around the terminal. Individual pieces of plant equipment can be identified by attaching RFID tags to them, operators scan the tags to ensure they are connecting the right loading arm or opening the correct valve.
Operators’ interest is maintained by gamification of checking order details. For example, a random list of customers is presented and the one relating to the order must be selected. For added safety, ATEX
hazardous area Zone 1 certified physical controllers can be optionally integrated to act as permissives.
The operator simply presents the smartphone with a successfully completed series of checks to a controller to activate a pump, open a valve, or release a locked gate. The smartphone app features several security considerations including PIN access, the ability to lock phones if they fail to synchronise with the server regularly, and encryption of data between the phone and server.
CheckScheme makes your data more meaningful. It provides managers with the ability to mine data from an audit trail to analyse day-to-day operations, red-flagging vulnerable areas so they can target improvements on the most error-prone or most used procedures. Find the cause of safety issues with instant analytics from your checklists.
Say “goodbye” to handwritten, unreliable and misplaced paper-based checklists.
benefits
Human Factor
security
QR codes
RFID Tags
Integration
Operational Insight
app
gamification
CheckScheme in Action
The CheckScheme solution includes a server which can either be deployed in the cloud or your own premises. Operation managers access the server using a web browser, and from there can configure and manage the site’s check schemes.
The CheckScheme app is installed on Android mobile devices, which are registered with the server over a Wi-Fi network. The Wi-Fi network does not need to cover the whole site, as the system is designed so that operations can be carried out without any immediate contact with the server.
When the phone is within range of the Wi-Fi network, it synchronises with the server, allowing the latest versions of the check schemes to be downloaded to the phone, and the activities the phone has performed to be uploaded to the server.
By installing the Wi-Fi access point in the staff canteen, the operators can hand in their checklists and can even receive changes to procedures while enjoying their morning cup of coffee.
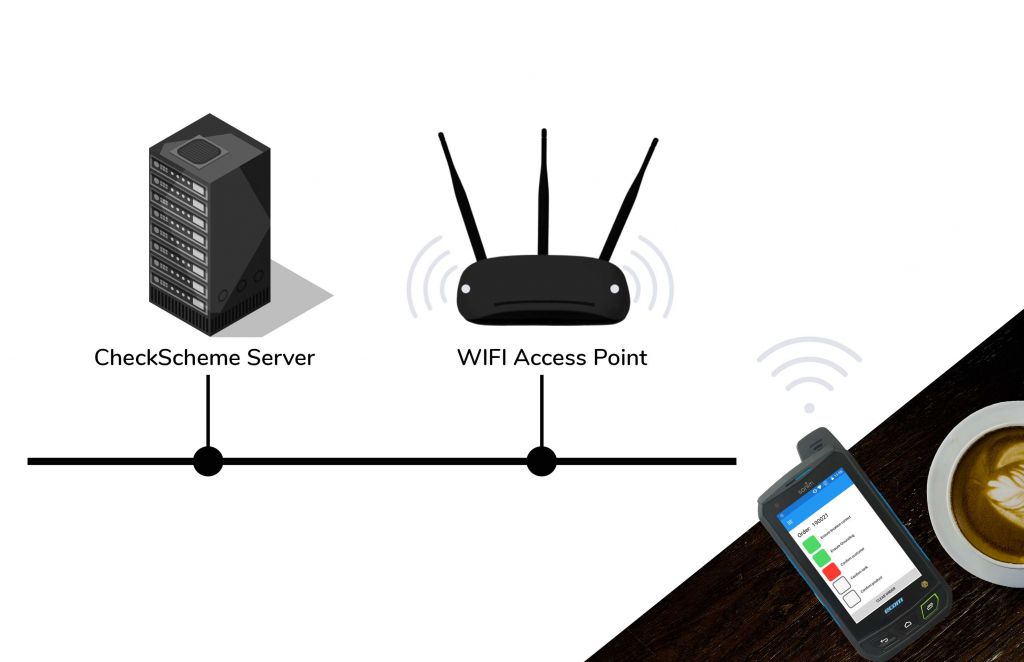
The latest features in CheckScheme allow for the recording of richer data and scheduling repetitive tasks. The system can still make use of RFID tags and QR Codes to identify locations and equipment, but now textual and photographic information can be recorded. For example, CheckScheme users can record photographs of the laden vehicles before they leave the site, to be able to show that they have discharged their duties in line with ADR and ensure every vehicle with a hazardous load leaves your site carrying the correct placards and markers.
The built-in calendar allows processes to be scheduled. Tasks such as manual tank dips can be scheduled to occur at regular intervals, capturing the levels recorded easily with the mobile device. An RFID tag placed on the roof of the tank which the device reads ensure operators can’t falsify readings. The server shows the results, permitting gauge drift to be assessed.
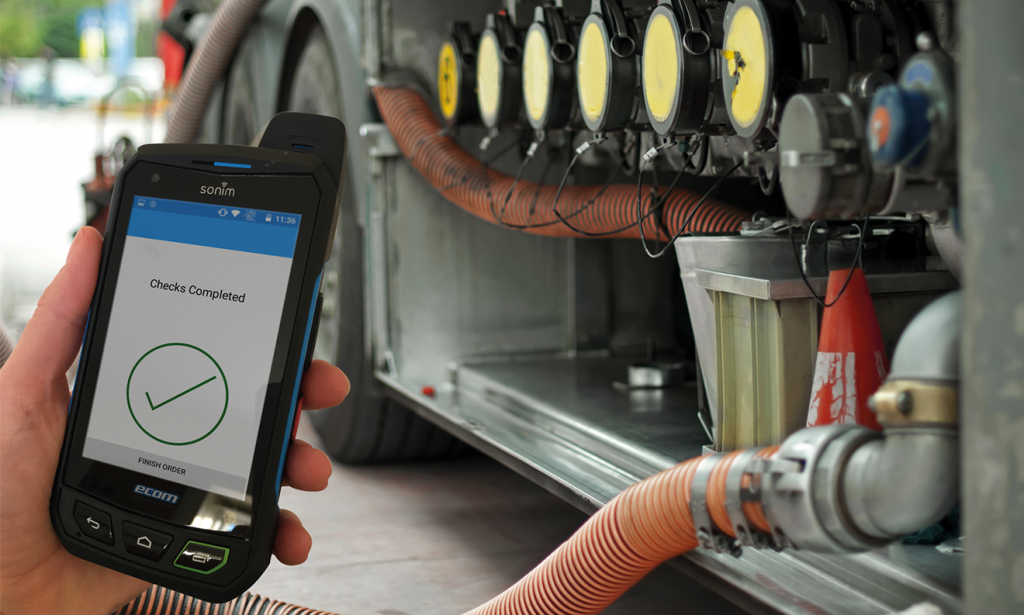
Managing processes
The data uploaded to the server includes a timestamped log of events that have occurred while using the app, including any incorrect responses the operator has given. Supervisors can examine the handling of a specific order to confirm issues regarding any delays in completing the procedure. They can also report statistics for the performance of
processes.
Check schemes are subject to workflow within the system. This gives the operations manager the ability to create a new check scheme, test it, then get it approved for use and retire old schemes at the end of their life. Paper-based systems, while being cheap to implement, are difficult to change and maintain. This leads to a reluctance to improve procedures, resulting in missed opportunities for safer and more efficient working.
CheckScheme is an outstanding digital solution. Not only because of how the algorithm and potential technology behind it has been maximised but also because of how the human factor has been at the core of the solution right from the beginning. When it comes to digitalisation, there is a great tendency to consider only data and technology, but MHT strongly believes the human element is of equal importance.
find out how checkscheme can help your site today
DATASHEETS
checkscheme
CheckScheme digitises paper-based checklists, enabling operators to carry out their checks
quickly and efficiently with an easy to use smartphone app.
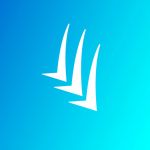
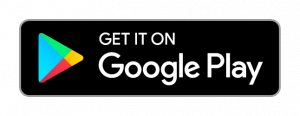